機械加工研究室
トップページに戻る

カウンタースタビライザー用のクイックディスコネクトを制作しました。'25 03/29
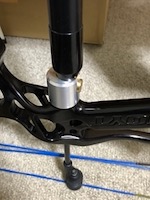
アーチェリーのクイックディスコネクトを制作しました。 '24 10/20
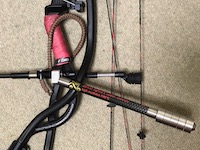
アーチェリーのスタビライザー角度を20度下げるアダプターを制作しました。 '24 09/13
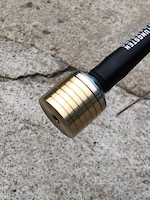
制作依頼があったアーチェリー用ウエイトを納品しました。5/16のネジ切りは流石にキツい! '24 02/24
スロットレーシングカーのタイヤを旋盤で回して、ヤスリを当てて整形しました。 '20 3/29
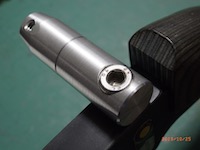
ちょっと不都合があったので作り直しました。 '19 10/25
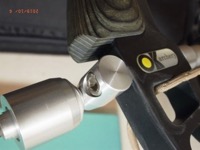
アーチェリーの道具を作りました。 '19 10/06
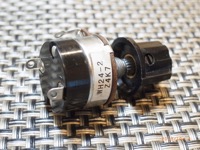
フライス盤のスピードコントロール(可変抵抗器)が変だなと思っていたら壊れました。
ネットで探すと同じものが専門店にあり、注文するとすぐに届きました。ネット社会はスゴイ! '19 10/04
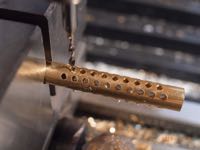
今年もエアコンのない部屋で工作です。φ1.6mmの穴開け。暑い! '18 08/05
この夏も工作です。 '17 09/17
凸部があり360度回せない部分も手回しハンドルを付けて旋盤を使います。 '16 09/21
.jpg)
工作室の引越しに伴って工具棚を作りました。これで探し回らなくて済みます。 '16 07/10
.jpg)
コンパウンドボウのリムボルトが貫通しているワッシャーが真っ二つに割れました。厚さ6mmのアルミ製です。
ちょうど良いサイズの端材があったので旋盤で挽いて完成。強度アップの為にテーパーは削りませんでした。 '16 03/24
自転車のサドル前に降りるとサイクルコンピュータに膝が当たるので、取り付け場所を少し前に移動しました。
上が今までのブラケットです。旋盤で部品を作り、フレームのキャリア取り付け穴に固定しました。
なぜハンドルに付けないかというと、20インチの車輪はセンサーの位置が低いので電波が届かないから。
'14 9/22
平目ローレットを買いました。こういう加工ができます。 '13 07/25
刃物台を傾けることでテーパー加工ができます。 '13 02/23
ローレット加工をもうひとつ。 '12 10/07
滑り止めにローレットを刻みます。斜めの刻みがあるローラーで上下から挟んで、工作物を低速回転させます。慣れれば簡単です。 '12 09/23
フライス盤は「塩ビ」パイプなどは簡単に加工できます。但ししっかりした固定が必要です。
'12 08/13
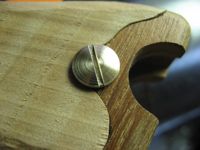
市販のマイナスネジは絶滅しているので自作しかありません。 '12 07/22
液晶TVの転倒防止金具を作りました。これをTVの裏に取り付け、ステンレスワイヤーをカーテンレールに通しました。 '12 03/21
エンドミルが届かない部分の溝加工はTスロットカッターを使います。 '12 02/25
円弧部分を削る為には、三つ爪チャックをセットしたロータリーテーブルをスライドテーブルに固定して加工します。
全高が高いのでドリルチャックは使えずコレットチャック(右)に交換します。
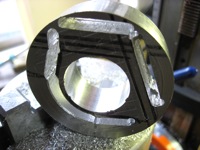
こういう加工に使えます。 '12 02/22
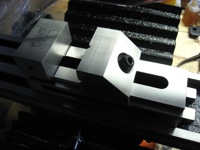
精密バイスを買いました。台湾製ですが精度は日本製のレベルに余裕で達しています。
各部の直角が高精度なので正確にスライドテーブルに固定できます。
斜め下に締め込むので軽い力で固定でき、浮き上がりません。通常のバイスはガタの分だけ浮き上がります。
'12 01/30
電動サンダーで1982年製フリッツハンセンテーブルのトップを削って塗り直しました。
30年使い込んだ痕跡をサンダーで削り、水性ウレタンニスを塗りました。
'12 01/10
昨日届いたフライス盤"X2"の慣らし運転を兼ねてアルミパイプの穴開けをしました。
こういった穴はフライス盤がないと、ドリルとヤスリでの格闘になります。 '12 01/07
アルミ合金(5056材)で内径に段があるパイプを製作します。
直径を6mm削るとこれだけ切り粉が出ます。
穴開けです。ドリルはφ12mmまでしかないので、それ以上は穴グリバイトを使います。
希望の大きさまで徐々に拡げました。材料が振れるので少しずつ削り4時間かかりました。
反対側の穴を開けました。 '11 12/29
真鍮のブロックを加工しました。大工事でした。下の部品を組み合わせます。
'11 09/09
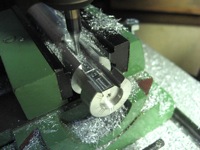
アルミの加工です。旋盤作業ではフライスのエンドミルも場合によってはバイトに流用できます。
ロータリーテーブルで分割線を描いて削ります。機械加工の楽しさが凝縮しています! '11 09/01
復活しました。 '11 04/13
注文の翌日届きました。ベルメックスインターナショナルのサービス対応はとても良いです。
'11 03/30
地震の後片付けに職場の研究室に行きました(今頃?)。
旋盤をテーブルに戻すと床に見慣れないものが! センターのハンドルでした。粉々です。
鉄板のトレイも曲がりました。今のところ旋盤はそれだけの被害です。
'11 03/28
愛用ミニ旋盤が地震で落ちました。 '11 03/11
刃物が食い込むので真鍮の切削はやっかいです。細いものを旋盤加工すると曲がる折れるの失敗の連続です。
バイト写真の下のように掬(すく)い角があると食い込むので、上のように鈍いバイトで削ります。
'11 01/26
滑り止めのチェッカリングの削り方です。まずは素材をバイスに固定し、45度に持ち上げて先端のチェッカーの一方向を削ります。
90度回して更に削ります。ピッチ1mmで削りますが45度傾けているので0.7mm程の送りピッチになります。
フライスの1目盛りは0.025mmなので28目盛りづつ進めます。深さは目測なのでルーペが必要です。
28の倍数を紙に書いておきますが80目盛りで0になるのでややこしいです。 '10 12/06
柱の縦溝をFluteと言いますが楽器のフルートと同じ綴りですね。これもフライス盤で加工します。 '10 11/03
φ2mm以下のエンドミルはよく折るのでまとめ買いをしました。 '10 05/10
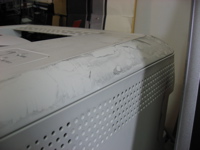
カーボンプレートをグラインダーで削ったら粉塵が部屋中を舞い、箱から出したばかりの新品プリンターが斑になりました。
静電気を帯びたプリンター外装が、見えない程細かい粉塵を吸い寄せたということです。
'10 04/12
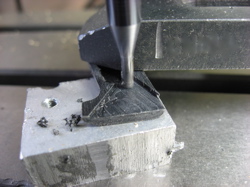
平らな凹面はフライス盤がないと大変です。
'10 03/26
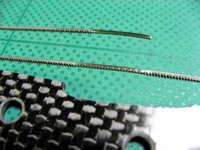
カーボンプレートを糸鋸盤で切りましたが、硬くて糸鋸の刃はあっという間に切れなくなります。
'10 03/13
フライス盤でも旋盤でも真鍮の加工は難しいです。鉄やアルミを加工している刃物で削ると、必要以上に食い込むことがあるからです。
専用の刃物を準備すれば良い訳ですが素人ではそうもできず、寸法精度がシビアな部分では「送り」を遅くすることで回避します。 '10 02/07
プロカメラマンから依頼のローアングルアダプター(フィッシュボーン社)改造です。
とにかく分解し、長穴を開ける部分のゴムクッションを切り取ります。
フライス盤にセットし加工します。穴の幅を調整し、段加工をします。組み立てて完成です。 '10 01/27
カーボン板の加工をしました。グラスほどではありませんが指がチクチクします。 '10 01/14
5056材で部品を作ります。56φから削るので卓上ミニ旋盤にはヘビーな作業です。希望の太さまで削って切り取ります。
チャックにセットし直して、15φの穴をドリル(13mmまで)と穴グリバイトで開けました。
フライス盤で更に削り、穴を開けてでき上がりです。
旋盤とフライス盤の連携で大体のものは作れます。 '09 9/26
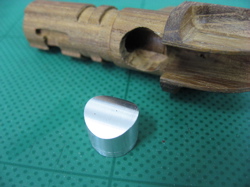
こういう2次曲面の複合体をアルミで作ります。
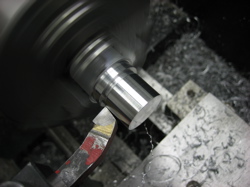
先ずは上面の曲率で円柱を作ります。
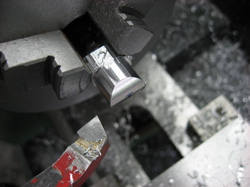
側面の形状をフライス盤で大雑把に削ります。削ったところを旋盤に銜え、側面を挽きます。
ひっくり返して反対側を挽き、不要部分を削り完成です。'09 5/28
フライス盤を使ったらあっさり削れました。黒檀は硬いと言っても所詮「木」です。 '09 3/31
ダークカラーの木材が必要で、黒檀を5mm厚に切り出したら硬くて、金属用のこ刃を3本折りました。結局プラ用刃の方が上手く切れました。 '09 3/22
木工の限界でしょう。穴φ12mm、外形φ13mmなので厚さは0.5mmです。手作業ではできません。 '09 3/09
木工が続きます。 '09 3/04
板厚調整です。 '09 1/16
下のは不要になったので木工を始めました。 '09 1/07
寸法を出しました。 '08 10/25
これのコピーを作ります。 '08 10/24
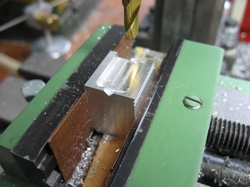
丸棒からパーツを作りました。フライス盤がなければ、ちょっとできない仕事です。 '08 7/09
パイプを作ろうとアクリルの丸棒の外径を削り、内径をドリルで開けると発熱で千切れてしまいました。
それではと、回転速度を下げて再トライするとまた同じことが起きました。とほほです!
よーく考えると、太いままの方が熱容量が大きいので〔軟化点80度ー100度まで達するのに時間がかかる)穴を先に開けてから外径を削ると上手く行きました。やれやれ! '08 6/12
アクリル板に同心円を彫り込む作業をしました。丸棒の端面に両面テープでアクリル板を接着し旋盤で削りました。失敗すると思いましたが最初からうまく行きました。'08 5/01
傾斜バイスによる斜面の切削です。任意の角度で削れます。'08 4/29
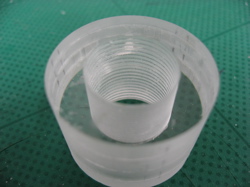
今日は楽しいネジ切りです。透明アクリルは細部が良く見えないし雌ネジなのでちょっと浅く仕上がりました。
アルミもネジ切りをしました。めでたくネジ込めました。'08 2/29
任意のサイズのアクリルパイプの作り方です。
外径を糸鋸で切り出し、必要な長さに接着します。
センターに穴を開け、ボルトを通してナットで締めます。
旋盤でボルトを掴んで外径を整えます。整えた外径を掴んで内径を削ればできあがりです。'08 2/28
真鍮は刃物が食い込むので注意が必要です。少しづつしか削れないので、このように太さの違いがあると時間がかかります。
今回は3時間かかりましたが、出来が良いと報われます。'08 2/27
ブッシュを3種作りました。
旋盤はネジを簡単に切れます。回り止めのローレットも切りますが、同じ外径でも力加減でこれだけ違うパターンができます。'08 2/26
フライス盤で木工が続きます。'08 2/20
今日は旋盤の基本工作をしました。'08 2/13
フライス盤では木工もやってしまいますが、木紛は金属粉と違って機械油を吸って細部に吸着するので良い事はありません。掃除が大変です。'08 2/12
糸鋸盤と一緒に購入した集塵機を繋ごうと思ったらサイズが合わず困りました。
糸鋸の方は「各種サイズに合います」という親切ぶった形状ですが、同じメーカーの集塵機が合いません。設計した人にお会いしたいです。
手持ちの塩ビパイプでアダプターを作りましたよ、RYOBIさん。'08 2/09
フライス盤による穴開けは、ボール盤より位置精度が高いです。小さい穴から順に大きくしていけば、その都度テーブルの僅かな移動で位置の修正ができます。'08 2/08
溝彫りが続きます。細いミルは負荷が掛かると左右に振れることがあるので溝より細いものを使い、ノギスで測りながら少しづつ作業します。'08 2/02
最終的にこんなに細くなりました。でも25φの外周面が後部凸の角です。
丸棒を角棒に削る作業は退屈ですが、溝彫りはフライス作業らしくて楽しいです!'08 1/28
反対側の面を削りました。25φの丸棒を6mmづつ削ったわけですが、さすがジュラルミンです。純アルミとは硬さが違い、舐めていた自分に反省です。'08 1/12
角柱の一面を削ります。これだけで2時間かかりました!!!
もう少し太いエンドミルで切り込みを深くすれば効率は上がりますが、所詮ホビーフライスなので、無理をするとプラスチック製のモーターギヤが欠けます。'08 1/11
角柱のセンターに穴のある部品を作るべく、丸棒から作り始めます。
四つ爪チャックがあれば角材から作りますが三つ爪チャックで四角い物は掴めませんから。'08 1/10
ロータリーテーブルにチャックを取り付けて内周加工をしました。外径も荒削りしました。'07 12/16
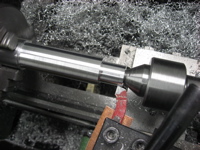
新しい工作の開始です。素材はジュラルミン2017(17S)の25mmφです。
反対側からの加工です。'07 12/10
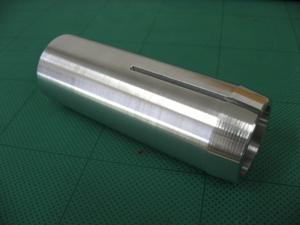
スリットをフライス盤で切削して完成です。
自転車に組み込んだ様子は自転車デザイン研究室にあります。'07 10/08
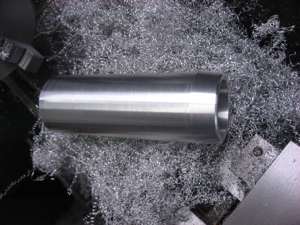
体積の60%を切り粉にして穴が貫通しました。もう一息です。'07 10/01
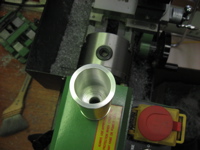
27.2mmφが入るように、最終的に27.3mmφまで拡げます。でも、穴ぐりバイトの長さしか掘れません。
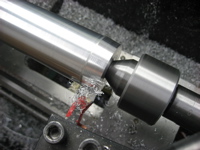
反対側をチャックにセットして、APBフレームのシートチューブから見える部分をテーパー状に仕上げます。
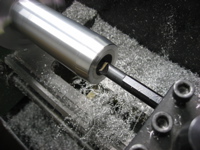
再度142~144往復して残りの穴を27.3mmφまで拡げます。'07 9/30
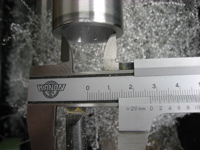
13φまで開けたら、次は穴ぐりバイトで更に拡げます。材料の片側しか掴んでないので無理はできず(振れてしまう)0.05mmづつ削ります。
27.2mmφまで142往復します(計算上です)。大量の細い切り粉が出ます。'07 9/29
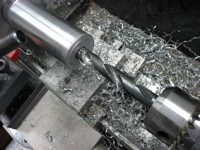
ドリルを徐々に太くし、最大径の13φまで使います。13φは加工材より長いので貫通できました。'07 9/28
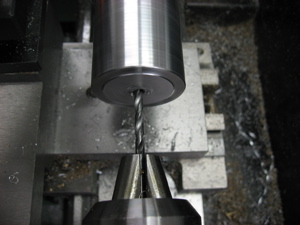
外径35φを仕上げました。
内径を開けるには細いドリルから始めます。いきなり太いドリルを使うと、音と振動がすごく、きれいに開きません。'07 9/27
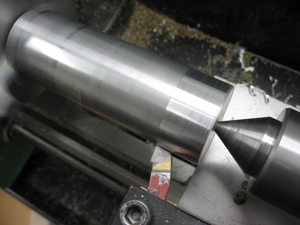
また依頼品の製作です。以前製作したモールトンAPB(自転車)用シートピラーシム(アダプター)です。
36φのアルミ(5056材)をセットし、センター押しの穴を開けます。
回転センターをセットし、35φまで切削します。'07 9/26
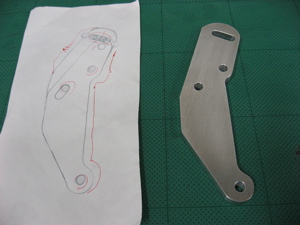
できました。機械加工研究室の割には手加工が多いです。'07 9/10
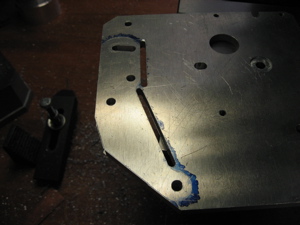
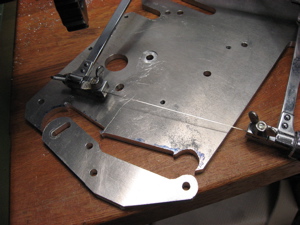
直線部分はフライスで削りますが、曲線部分は糸鋸です。小一時間汗をかいて切り取れました。電動糸鋸を買いましょう。'07 9/06
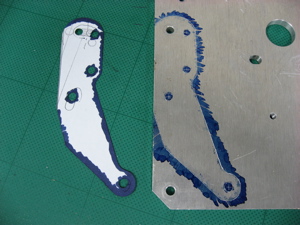
久々の金属加工です。依頼品ですが図面が「それなり」なので適当に作ります(うそです)。
原付のブレーキホルダーなので真面目に作ります。寸法がないので図面を切り抜き素材にトレースしました。
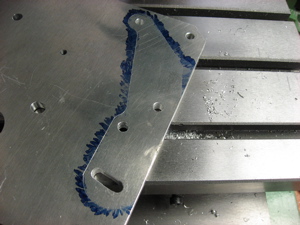
とりあえず穴開けをします。'07 8/29
異種金属の組み合わせで一体物が作れます。
公差を取らない凹凸(手の力では入らない程度)をバイスで圧入します。'07 7/08
アクリルの長穴加工は楽しいです。'07 6/11
溝、長穴、単純な穴開けなど。真鍮加工はきれいで楽しいですね。'07 6/06
曲面をコーナーRカッターで切削しますが、硬くてアルミの3倍時間がかかります。'07 6/05
エンドミルの長さが厚さ10mmに足りないので裏からも切削します。
切り離す前に穴などの細かい工作を済ませておきます。'07 6/02
真鍮を加工しますが10mm厚は値段が高いです。100mm*100mmで¥3000を越えます。
図面を型紙にフライスで削り出します。外形を切るのに、最初、金工糸鋸を使いましたが2mmほど切ってやめました。硬いです。'07 6/01
まだまだ、アクリルの加工が続きます。'07 5/28
アクリルの加工が続きます。'07 5/24
凸部があって旋盤で回せない工作物はフライス盤+ロータリーテーブルで切削しますが、フライス盤のテーブル長を越える場合は、旋盤に手回しハンドルを取り付け切削します。
アルミならなんとか削れます。'07 5/15
更に作業は続きます。'07 4/27
回転センターで固定し、旋盤の基本切削が続きます。
この6063というアルミ合金は建築サッシ使われる耐蝕性に優れた素材ですが、切り粉が繋がってしまい旋盤の作業性は悪いです。'07 4/26
金属加工の再開です。長さ300mmのアルミ素材を加工するのに、チャックの反対側をセンタードリルで穴開けする訳ですが、
ドリルチャックを入れるスペースがありません。センター間300mmの旋盤ですが300mmは加工できないということですね。
今回は半分しか使わないので切断すれば良いのですが、バンドソーは持っていないし、そうかといって金鋸で切るのも大変なのでフライス盤で切りました。
その後センター押しの穴を開けます。'07 4/25
傾斜バイスを使うと任意の角度で削れます。溝掘りもフライスの得意分野です。'07 4/20
こういう宮大工のような加工は精度的に機械が有利です!'07 4/16
最初は木工からになりました。サクサク削れて楽ですが掃除が大変です!'07 4/13
いよいよ工作室が始動です。'07 4/02
かなり片付きましたが、工作機械はまだこんな感じで使えません。一人で動かせないし!'07 3/29
引っ越して来た工作室ですが、荷物で身動きがとれません。一個足りないし!
とりあえずIKEAの時計を掛けましたが電池が無くて動きません。'07 3/26
工作室の引っ越しなので二週間ほど作業がストップです。こんなこともあろうかと木箱を取っておいてよかった!'07 3/14
フライス盤は工作物の固定が重要ですが、例えばバイス(万力)で歪んでしまう「コの字断面」のもの等は補強の中子を製作し内部に入れます。'07 3/02
フライス盤は細長いものを縦にバイスで固定しても、動いてしまうので加工し難いです。でもアクリル樹脂は切削しやすいので、低速で慎重にやればなんとかなります。'07 2/26
曲面は階段状に切削してからRタイプのエンドミルで仕上げます。'07 2/13
球面は専用の「姿バイト」を作ります。同じ形の量産ができます。07 2/09
金属以外も加工するので「金属加工研究室」を改め「機械加工研究室」となりました。'07 1/30
長穴を加工しました。やはりフライス盤より糸鋸盤のほうが遥かに速いです。でも、仕上げにフライスで一回さらいます。07 1/22
アクリルを加工しました。ABSのように切削熱で溶けないので作業性はいいのですが、板材の切り出しは糸鋸盤のほうが遥かに速いです。'07 1/16
初めて銅を加工しましたが、粘りが強くビビるので作業時間がかかります。06 11/28
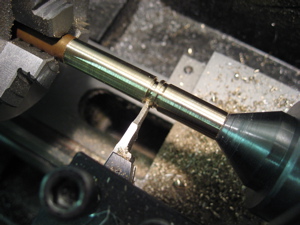
久々に加工開始です。06 11/27
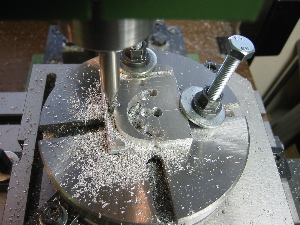
ロータリーテーブルが活躍し、円弧が自由自在です。06 9/01
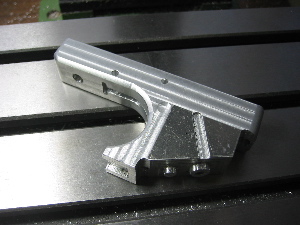
21日のものが完成しました。何に使う部品かは想像にお任せします。06 8/29
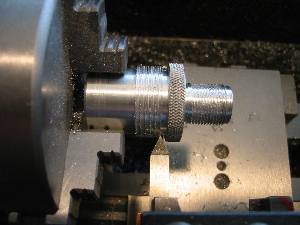
ピッチ違いのネジ切りです。ギアの組み替えが面倒です。ローレットは上手くできました。06 8/22
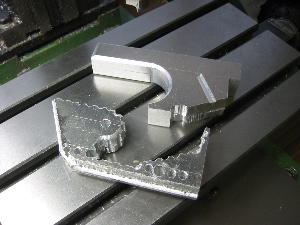
下穴は切り子の逃げ道になり、切削の抵抗も減るので、剛性不足のX-1でも使い方次第ということです。06 8/21
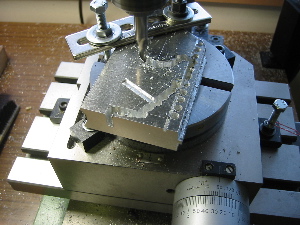
厚い材料をフライスで切り出す場合はドリルで下穴を開けておくと楽です。曲線はロータリーテーブルで。'06 8/10
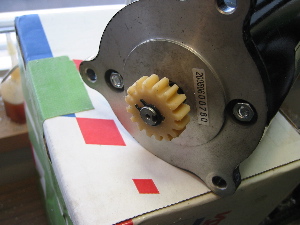
あー!やってしまった。ちょっと無理なことをしたらモーターギアを壊しました。3回めです。メカヒューズなので仕方ありません。予備部品に替えて再開です。'06 8/08
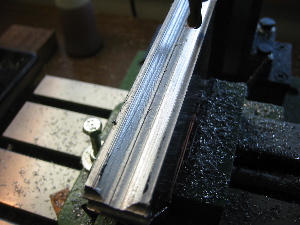
曲面を切削します。普通のエンドミルで階段状に削り、Rのエンドミルで仕上げます。
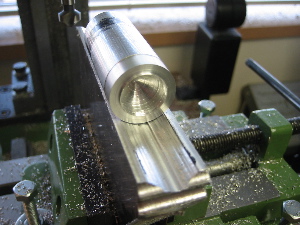
円筒状の物がフィットする溝ができました。'06 8/07
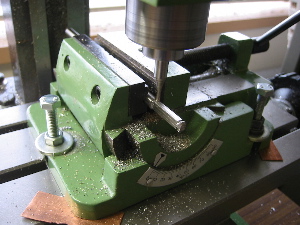
ステンレスの加工です。アルミや真鍮より格段に硬い素材です。旋盤加工の後、フライス盤で加工します。
加工の便宜上、最後に素材から切り落とします。'06 7/27
おなじみのネジの製作行程です。
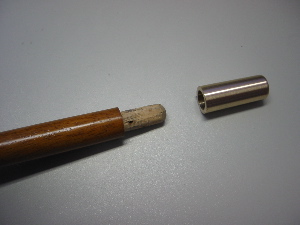
傘の石突きも製作しました。'06 7/26
部分的な出っ張りは周りを削って作ります。'06 7/21
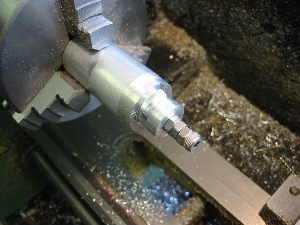
小さなパーツの加工は専用のホルダーを作ります。今回は四角い素材を円弧に削ります。
設計寸法通りにできました。加工物が小さくてもホルダーはガッチリ作ります。'06 5/18
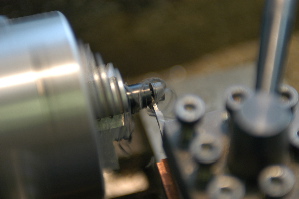
ABS樹脂も加工できますが、切り子が絡まり作業しにくいです。'06 5/08
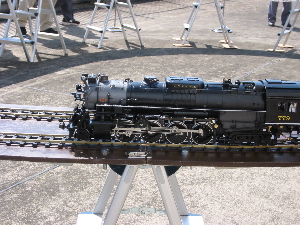
こういうおじさんたちって、旋盤やフライス盤のヘビーユーザーです。鋳造なんかもやってるに違いありません。横浜ハンズの屋上って初めて上がりました。'06 5/03
アルマイトを外注し、タップを立て、組み立てて完成です。
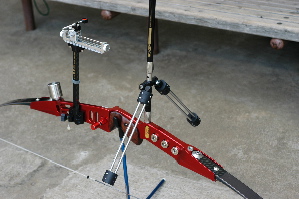
弓に取り付けた状態です。ロッドはステンレスの無垢なのでゲキオモです。'06 3/25
いよいよロータリーテーブルの登場です。90度づつ回して穴を明けます。
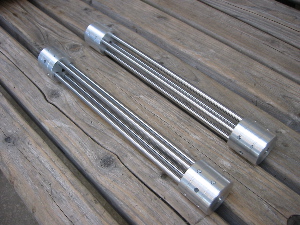
ロータリーテーブルを横倒しに固定して、側面の穴を90度づつ回して明けます。完成です。こんな感じに組み立てます。'06 3/10
同じものをもう3個作りました。ロータリーテーブルの登場は次回です。つづく!'06 3/06
アーチェリーのスタビライザーパーツの製作です。ロータリーテーブルの初仕事です。
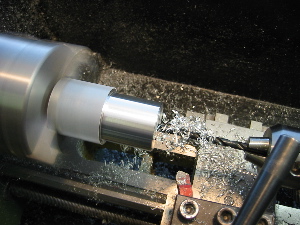
素材を希望のサイズまで切削します。端面処理と面取りを済ませます。センターの穴明けをします。
ネジ穴の位置に溝を彫ります。突っ切りバイトで切り落とします。ロータリーテーブルの登場はまだです。つづく!'06 3/05
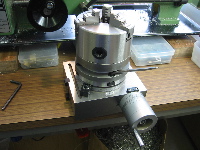
チャックを逆さにし、製作したスペーサーを載せます。取り付けプレートを載せてボルト留めし、ロータリーテーブルに載せます。
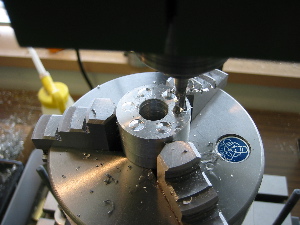
スペシャルツール(ヘキサゴンレンチをカットしたもの)でボルト留めします。チャックで固定した素材を正確な角度に回して切削できるので、あんな物やあんな物が作れます。'06 2/27
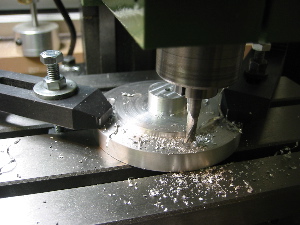
左側も切削します。バイトホルダーとの位置関係から、切削作業できる最大径なのが分ります。穴明けはフライス盤で行ないます。
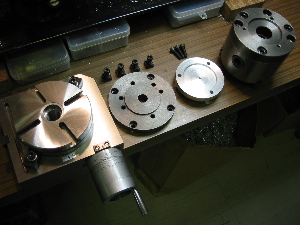
100φのロータリーテーブルに100φのチャックを取り付けるのは、どう考えてもレンチの入る所が無いので80φのスペーサーを製作した訳です。つづく!'06 2/24
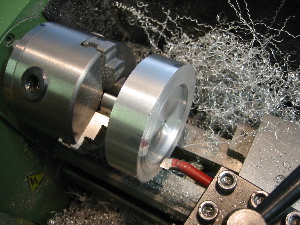
ロータリーテーブルにチャックを取り付ける為のスペーサーを製作します。
80φもある材料は私の旋盤のチャックでは掴めないので、掴むパーツをネジ止めします。
外周と右側を切削しました。 つづく!'06 2/23
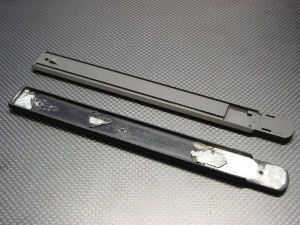
二ヶ月ぶりの金属加工です。下の部品の代わりに上の部品を使いたいのですが、裏側の形状が全然違い、このままでは取り付けられません。
そこでフライス盤の登場です。亜鉛合金ダイキャスト製なのでアルミより加工し易いのですが、全体を掘り込むのでクランプ場所を数回変える必要があり2時間ほどかかりました。'06 2/20
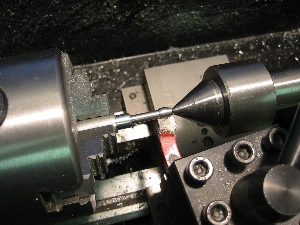
リューターチャックの内部部品の製作です。
このような小さな部品は旋盤チャックで固定すると手加工も楽です。写真は糸鋸での作業。'05 12/22
金工と木工を合体。
'05 12/16
卓上フライス盤は、写真のような小さなスペーサーなどを、必要な時にすぐ作れて便利です。
'05 12/13
また木工です。バンドソーとサンダーで外形を削り、細かい所をフライスで仕上げました。全ての行程が電動工具で済んでしまうので楽々です。
'05 12/02
外径が大きく短いネジ切りはチャックの爪が邪魔で正面からバイトが入りません。
半日考えて、内径用ネジ切りバイトで反対側から逆回転で切ることにしました。逆ネジにはなりません。
'05 12/01
久しぶりの旋盤作業ですがフライス盤と違いほっとします。フライス盤は旋盤の3倍難しいです。
アルミのパイプを加工しましたが市販の素材は真円度が低く外径と内径のセンターも合っていません。真鍮パイプのねじ切りもしましたがこれは楽しいです。
'05 11/29
カーボンFRPの加工をしました。ラジコン模型用として販売されていた素材で、表面はカーボンですが中間層はグラスでした。削り始めはカーボンの黒い切り子ですがその後白くなるので判ります。手もチクチク痛いし。実用上は問題ないですがフェイクですよ横浜○急ハンズさん。
因みに自動車の非純正カーボンパーツの多くは同様にフェイクです。
'05 11/28
アルミの黒染めです。今回はバーチウッド社のアルミブラックを使用しました。
事前に洗剤で充分に脱脂します。亜鉛のように、塗ってすぐ黒くなる訳ではありませんでした。
綿棒でアルミブラックをこすり付けるように塗り込み、ひととおり黒くなったところでドライヤーで乾燥させ水洗します。少し色落ちするのでもう一度塗り込みます。乾燥後オイル仕上げします。真っ黒ではない、いい感じの黒になります。
'05 11/18
木工も楽々です。が、後始末が大変です。
'05 11/16
ロータリーテーブルを使いました。工作物が大きいとクランプが大変です。
今回の加工です。
'05 11/14
左の黒い物のコピーが完成しました。形状は少し違いますが機能的には同じ物です。
今回は、かなりのノウハウを得ることができました。
'05 11/12
今回はこの傾斜バイスが役立ちました。
複雑な切削をする場合は、作業の順番を良く考えないと最終的にバイスやクランプで固定できなくなります。これを「段取り」と言い、じっくり考える人に向いています。そそっかしい人はだめです。
'05 11/10
このフライス盤のような入門機は剛性が低いので刃先が振れ易く、溝を切削するような場合、出来上がり寸法より細いミルを使います。希望の深さまで切削し、更に側面を仕上げて幅の寸法を出します。
'05 11/08
夏休みの工作第7弾はまだ完成に至っていませんが、臨時の工作が始まりました。
図面も描いて切削開始。やってますよ○野さん。
'05 11/07
フライス盤用ロータリーテーブルと三爪チャックが届きました。
フライス盤は工作物を前後左右に移動して切削しますが、これを使うと正確な角度に回転させて加工できます。円周上に等間隔に穴を開けるとか、円筒の外周に溝を彫るとか、旋盤ではできない出っ張りのある円筒を作るとか、工作範囲が広がります。
防錆油がギトギトなので、詳細写真はまた後日に。
'05 10/31
明らかな弱点なので、良い対策はないのか電話で聞くと「また送りますから」とのこと。2個送られてきましたが、対策?
外して改めて見ると酷い壊れ方ですね。
'05 10/26
フライス盤が使えないので今日は旋盤を使いましたが、1年ほど経験を積んだので作業が早くなりました。
フライス盤はまだ初心者ですね。
'05 10/25
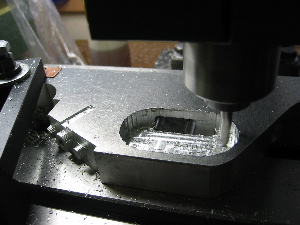
新しいギアが届き作業再開です。
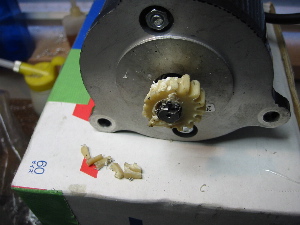
4時間ほど調子良く作業し、10mmのミルに替えたところこの有様です。歯が半周以上無くなりました。
また電話しました。とほほ!'05 10/24
欠けたギアでは、やはり作業は無理で、部品待ちです。
'05 10/20
フライス盤でも穴明けにはドリルの刃が使えます。コレットチャックの径と合う刃だけですが、ボール盤より位置精度が格段にいいです。
'05 10/19
やはりモーターのギアが欠けていました。同時に空転止めのKeyが外れていました。
保証期間なので販売元にギアを請求しました。幸い窓口の女性は対応が良く、部品番号を即答しましたので、頻発しているようです。Keyを組み直したらなんとか使えそうなので作業再開です。
'05 10/18
フライス盤の調子がおかしいです。
負荷をかけるとモーターは回っているのに刃物が回りません。ギアで減速しているのでスリップではない筈ですし、保護回路が働いた場合はモーターはストップします。ギアを舐めたか?
'05 10/17
3日かかった切断作業が終了しました。
高熱のため切り子が付着したり、表裏のズレた切断面は、フライス本来の作業で仕上げます。
'05 10/14
フライス盤で立て続けにエンドミルを2本折りました。焦りは禁物です。
という訳で、写真はありません。
'05 10/13
「板もの」はフライスで切ってしまいますが、厚いと時間がかかります。
'05 10/11
スプリングが強過ぎました。
'05 10/07
球面もなんとかできます。
フライス盤が強い味方です。これがないと大変な作業です。
'05 10/05
パイプのネジ切り達人になりました(写真左)。
ローレットも目的の形ができるようになりました。やはり、ローレット駒のピッチと工作物の直径は関連があって、適当にやってもダメなようです(写真中)。
パイプ形状の集合体ができつつあります。
'05 10/04
ジュラコン(ポリアセタール樹脂)を加工しました。旋盤の練習にいいかも。
部品がかなり揃ってきました。
'05 9/29
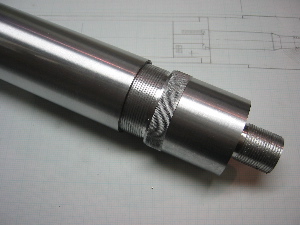
パイプ内面のネジを切削します。旋盤の能力限界(寸法的)の加工なので、各部のクリアランスがギリギリです。
こういった工作は、金鋸やヤスリのレベルでは全くできません。
'05 9/28
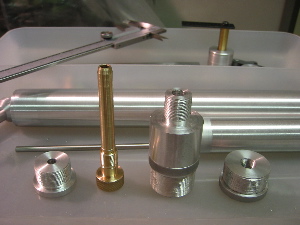
旋盤のネジ切り作業は楽しいです。
'05 9/27
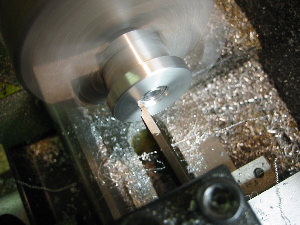
複雑な形状は自作バイトで加工します。
'05 9/26
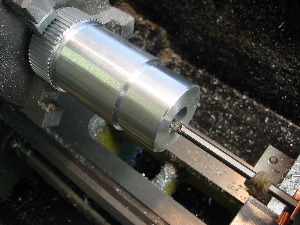
夏休みの工作第7弾。
長いパイプは旋盤にセットできないのでフライスでカットします。
パイプの表面を切削する場合はセンターを押せないのでキャップを製作します。チャック側も潰れないように中栓を製作します。
穴の内面を仕上げるのに内径バイト(穴グリバイト)が役立ちます。
'05 9/21
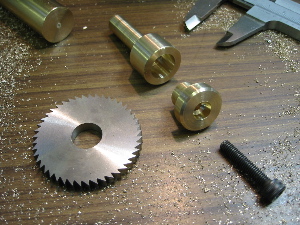
夏休みの工作第6弾。先日購入した45φフライスカッターのホルダーを製作しました。今回は真鍮で。
'05 9/11
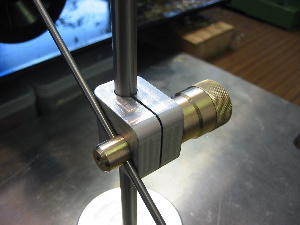
夏休みの工作第5弾、トースカンを製作しました。定規で測れない部分の高さを測ったり、2点の高さを比較したり、定盤に対して平行な線を工作物に引いたりします。固定できる「けがき針」ですね。(ステンレス、アルミ、真鍮)
'05 9/08
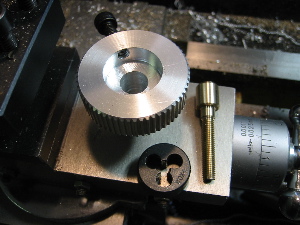
ダイスホルダーを製作しました。旋盤でダイスを使って雄ネジがまっすぐ楽に切れます。
右の写真がホルダー、ダイス、製作したネジです。
'05 9/05

購入したコーナーRカッター(R5)を使ってみました。3往復程度で半径5ミリのコーナーRが切削できます。
'05 9/02
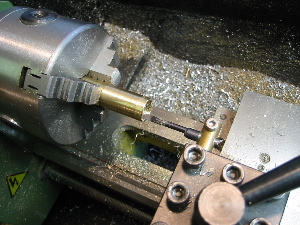
買ってあった内径ネジ切りバイトのホルダーを製作し使ってみました。内径やピッチが自由自在です。
'05 8/24
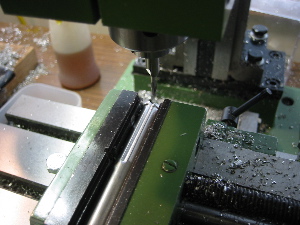
ピープサイトのストリングに嵌める溝もフライスで簡単に彫れます。
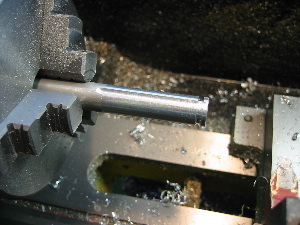
輪切りにしてすり鉢状に削ります。
'05 8/16
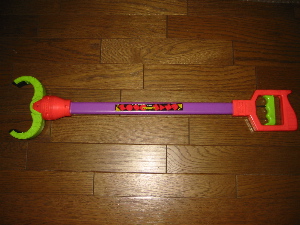
こんなものになりました。左ハンドルの車は駐車券や通行券が取れないことがあるので、こういうものが必要です。自転車のハンドルとブレーキレバーを流用しています。右は今まで使っていたもの。
'05 8/11
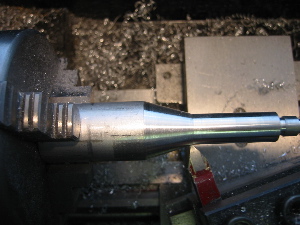
トップスライドを傾けられるのでテーパー切削ができます。
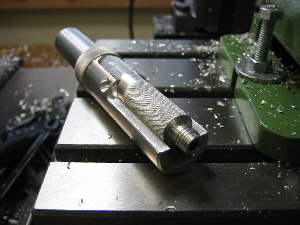
今、製作中のもの。テーパー部分は内部にあります。'05 8/04
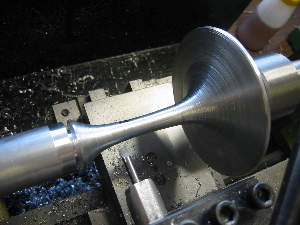
描き出したガイドを目安に支柱を削ります。底部と合体させて形が合うように更に削ります。
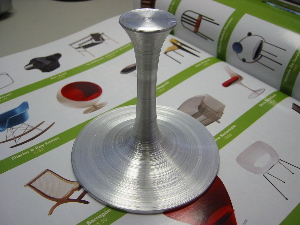
ゲージで形状の確認をして脚部の完成です(上半身に続く)。'05 7/28
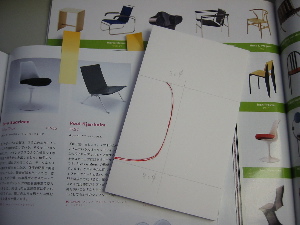
今回は赤い座面のこれを作ります。脚部の素材は80φのアルミです。写真から形状を描き出します。
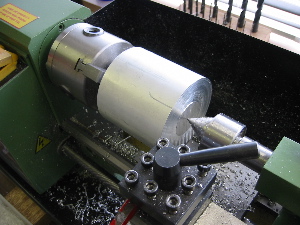
私の旋盤のチャックで掴めるのは70φまでなので、掴む部分を作りネジ留めします。バイトホルダーぎりぎりなのでこのサイズが限界です。チャックと同じ太さです。
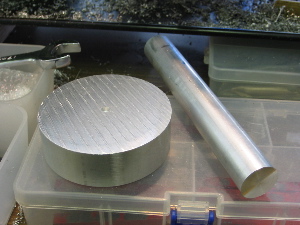
でも、良く考えると90%以上を切り子にしてしまうので資源の無駄使いだし、忙しい私には(えっ?)時間が勿体ないので、底部と支柱の2部品の組み合わせで作ることにしました。
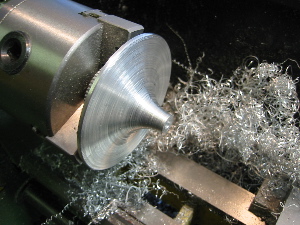
描き出したガイドを目安に底部をせっせと削ります。
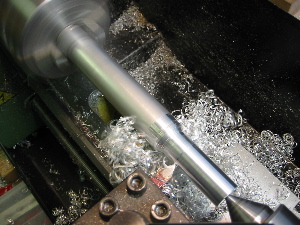
こんなものになりました。支柱部分も削ります(続く)。'05 7/25
素材の形状に合わせた固定方法を工夫すればバイスなしでもいけます。固定治具を作ってしまえばいい訳ですから。
今までは金鋸とヤスリで格闘していたことを、あっという間に加工できるようになりました。夏休みが楽しみです。'05 7/14
ボール盤の「おまけバイス」を取り付け、フライス盤の試運転です。ハハハハー、削れる削れるー、サクサク削れます。もっと早く買えばよかった、という感じに削れます。
このバイスはいいかげんなので、素材が動いてしまって正確な寸法が出ません。'05 7/11
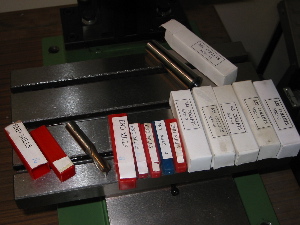
買い物メモのようにフライス盤がやっと届きました。我が密造工・・・じゃない研究室もこんな感じに充実してきました。
刃物も揃ったのですが、加工物を固定するバイス等を発注していなかったので,
試運転はまだです。'05 7/08
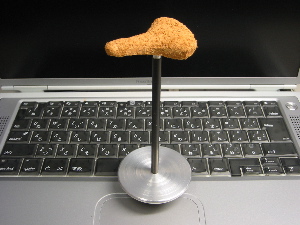
こういうものになりました。詳細は「椅子のスケールモデル」に。'05 7/01

こんなものができました。旋盤作業はここまで。'05 6/24
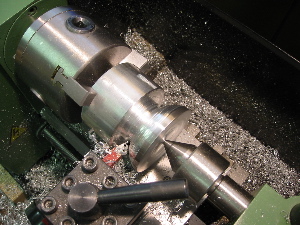
どんどん削ります。形が見えてきました。'05 6/23
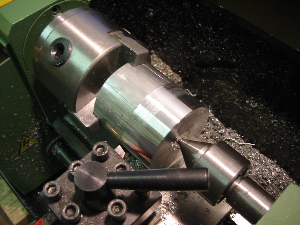
今までで一番太いアルミ(60φの5056)を削り始めました。
一部の人が期待しているものを作っているのではありません。'05 6/22
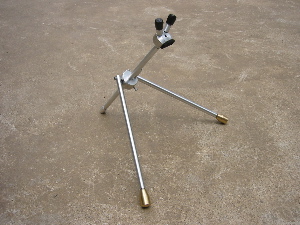
アーチェリーのボウスタンドを改良しました。詳しくはアーチェリーの話にあります。'05 6/18

ボーリングホルダーを使いました。穴の内面が非常に綺麗に仕上がります。
この後の作業を失敗し、この素材はお釈迦になりました。トホホ!'05 6/02

アーチェリーのボウスタンドを製作しました。主な素材はジュラルミン2017。使い方はアーチェリーの話にあります。'05 5/28
いつの間にか集まった(買ったんですけど)素材を公開。ジュラルミン、ブラス、ステンレスなど。'05 5/19

メタルソーを使いました。高速回転ではとんでもない騒音なので低速(毎秒3~4回転)で使いました。電気モーターは低速でもトルクがあるので手挽きのような音で切削できます。切り口を見ると低速の方が綺麗です。'05 4/20
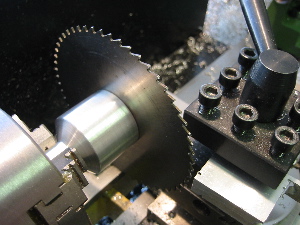
ヤフオクで購入した中古メタルソーのホルダーを製作しました。本来なら鋼材を使うべきですがアルミや真鍮しか加工しないのでアルミ(ジュラルミン)で作りました。
まさに旋盤加工の基本で、今までの経験(たいしたことない)を総動員という感じです。
旋盤に取り付けると「何でも切ったるでー」となぜか関西弁の乗りです。'05 4/08
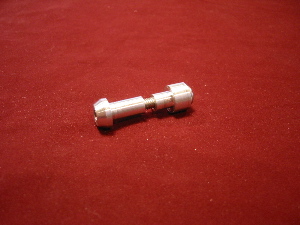
自転車のシートピンを製作しました。小型化、軽量化です。詳しくは自転車デザイン研究室にあります。'05 3/12
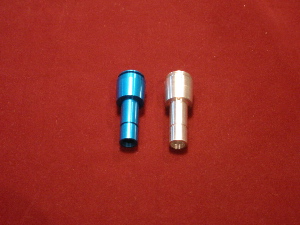
テーパー加工の試作の為、市販部品(青い方)の複製をしました。これで3時間の作業です。'05 3/04
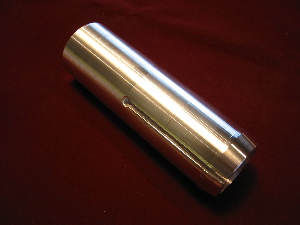
ピラーを締める為の切れ込みを入れました。このジュラルミンは7075らしいのですが、金鋸で切ると普通鋼(軟鉄)と同じくらいの硬さで一汗かきました。やはりフライス盤が必要です。
それから、自転車に組み込みました。その様子は自転車デザイン研究室にあります。'05 3/03
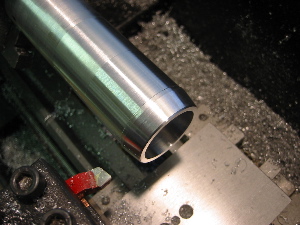
最後に、自転車に組み込んでも外に見える部分を仕上げます。'05 3/02
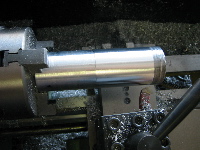
反対側から貫通しました。今度は外側を、自転車のシートチューブの内径φ35mmまで半分削ります。薄汚い素材がぴかぴかになります。また左右入れ替えて残りの外側を削ります。今日はここまで。'05 2/28

φ27.1mmまで拡げました。バイトの長さの関係で貫通できないので、左右をセットし直して同じことをやります。今日はここまで。'05 2/25
「買い物メモ」のシートピラーを使う為のシム(アダプターのこと)の製作を始めました。
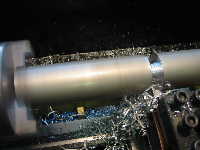
φ36mmのジュラルミンをくわえる為にチャックの正爪を逆爪に交換します。
この旋盤のキャパ最大の300mmの材料を必要な長さにカットします。結構大変です。
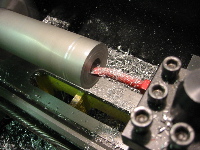
φ27.2mmの穴を開ける為に、細いドリルから順に太くし、穴ぐりバイトで更に拡げます。今日はここまで。'05 2/22
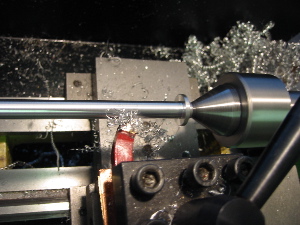
新作二点(ジュラルミン)。実用になる機械部品もサクサク作れるようになりました。とにかく楽しい!'05 2/02
ストリングに嵌める溝を彫り完成です。'05 1/30
「アーチェリーの話」に取り付けた写真を載せました。'05 2/05
下のピープサイトより厚みのある2作めを製作しました。持ち合わせのバイトでは深く彫れないので,またバイトの自作です。先日穴グリバイトを作った時のヘキサゴンレンチの切れっぱしをアルミのシャンク(ただの端材の角棒)に取り付け、グラインダーで成形しました。結構切れますが普通の工具鋼(たぶんSK)なので頻繁に研ぐ必要があります。
右の写真は、シャンクの上に出来上がりを乗せたもの。'05 1/26
コンパウンドボウのピープサイトを真鍮で製作しました。詳しくは「アーチェリーの話」に。'05 1/22
ドリルチャックはφ13までなので、それ以上の穴は穴グリバイトを使いますが,
使用頻度は低いので買うほどではなく、4mmのヘキサゴンレンチをグラインダーで削って作りました。ジュラルミンは問題なく削れましたので、同じように内径ねじ切りバイトも作れそうです。'05 1/21
ステンレス(SUS303)の加工を行ないました。SUS304のほうが腐食に強いのですが、この303のほうが旋盤加工に適しているそうです。でも海水にでも浸けないと錆びません。サクサク削れるのですが切削面が荒れています。バイトの研ぎ方を研究する必要があります。
できたのはピンポンチ3φです。写真のようなピンを抜くのに使用します。'05 1/14
慣らし運転も終わったようなので、気になっていたトップスライドのガタ調整をしました。アリ溝に嵌めてあるジブ(通称カミソリ)を押しているイモネジとそれを固定している7mmナットで調整します。イモネジで(ヘキサゴンレンチを使う)ガタ調整をしても、ナットを締めるとガタが少し出るので微妙です。しかも3か所あります。エンジンのタペット調整みたいな要領ですね。'05 1/13
初めて「使える」道具を作りました。バイト刃高ゲージです。カーボン板の下面を回転センターの高さに合わせていて、バイトの刃高をここに合わせます。これを疎かにすると、滑って削れなかったり、食い込んだりします。'04 12/16
銅板を挟んで偏心させた溝彫りをやってみましたが、バイトが折れました。そんなに無理してないのですが。
ネジ切りもやってみました。自動送りの親ネジを回転させるギアの組み替えが必要です。今回は径12.7mm、ピッチ1mmのネジを切りました。メートルネジなのでバイトの刃先は60度のものを使います。旋盤ではタップやダイスを使わずに自由な直径、ピッチのネジが簡単に切れます。'04 12/02
穴開けをやってみました。ど真ん中にまっすぐ開けるのは旋盤しかできません。
ドリル刃の螺旋の意味が良く解りますね。'04 11/29
自動送りを試しました。切削中は見ているだけなので、写真を撮る余裕ができます。自動なので奇麗なバイト目ができますね。ピカピカで楽しい。'04 11/25
アルミを削りました。まずセンター押しの穴をセンタードリルで開けます。ドリルチャックが回らないのは新鮮な光景です。それから回転センターで押して切削です。切り粉が盛大に出ますが、シュルシュル削れて気持ちがいいです。'04 11/20
「買い物メモ」で紹介した旋盤導入後の初加工レポートです。真鍮製のウェイトのネジ部の削り落としをやってみました。中古で買ったアーチェリー用のスタビライザーのウェイトですが、前のオーナーがペンチのようなもので切り落とそうとした痕跡のあるネジをバッサリ削りました。バイトが0.5mmほど低かったので直径1mmほどのへそが残りましたが、スペーサーを入れて再度削り完成です。例のバイブル「ミニ旋盤を使いこなす本」にある「すくい角のあるバイトは食い込むので真鍮には向かない」ということを体験しました。振動が出るので真鍮専用のバイトが必要です。
今回の作業を金鋸やヤスリでやると、こんなに綺麗にはいきませんね。加工物に傷をつけないように真鍮の薄板を巻いて三爪チャックにくわえています。'04 11/11